TANIO / IGNITE
Incubation Project - Working with Aberystwyth University’s Ceramic Collection
The Incubation project at Aberystwyth University, titled TANIO/ IGNITE. I chose to respond to the topic of Swansea and Nantgarw porcelain. To which brought together the latest industrial manufacture and technology coupled with artisan knowledge and leading craftsman of the 19th centaury. Producing pieces of porcelainware that were compared and equalled to Sèvres porcelain, France.
In which they produced vases, dinner services and tea sets with simply elegant forms which have stood the test of time, being domestic ware that is symbolic of status and antiquity. Within this attempt to rival the French porcelain, Swansea porcelain, although beautifully translucent when fired. The porcelain mixture, due to its glassy nature, was unstable and warped most outcomes.
I believe the coupling between artisan knowledge and the latest technology of the time, to produce ceramics, speaks of my own practice. In which, I am using traditional mould making and slip casting processes in connection to 3D scanning, digital modelling and printing. Which allows the replication of these archetypal shapes with the intent to cast, that would otherwise be hard to obtain due to them being on display in museums, such as in Cardiff.



Digital applications enable the virtual play of elements proportion and combination in the aim of producing new and exciting objects; transcendent of the originals. Brought into reality and ceramic with my experience in 3D printing, casting and mould making to achieve a high finish of reinvigorated slip-cast porcelain ware. I was keen to call attention to the simple elegance of the work, striping back these symbolic archetypal forms of antiquity which were originally heavily embellishment with the decorated surface. Although, not losing the exterior narrative of the traditional pieces, but replacing it for a materialist narrative. Due to the lack of Nantgarw porcelain, although recently being revived from the coded recipe, I will be using bone China. Although not being as translucent as the unique Nantgarw porcelain, it will still give me the material qualities that I am after; thin, fragile, brilliant white and a material memory that will distort and warp.
Within my research, I have been drawn to the theories of new materialism and emergence within the making practises. In which material matter possess its own modes of self-transformation, organization and thus no longer inert and passive to the maker. Establishing making as a process of growth immersed in a world of material, which the active maker ‘joins forces’ to uncover an object. A world where things are continuously coming into being through processes of growth and movement. With these ideas in mind, I was looking for the work to speak of industrial craftsmanship with perfectly cast porcelain forms set in relation to material qualities, movement a growth. Translucency, warping and melting; all giving gesture of the Bone china’s materiality. Originally seen as the failure of the factories of Nantgarw and Swansea, where the ideal was to control the disobedient material.
This work aims to challenge this thinking with objects that are perfectly imperfect, in an unstable balance. In order to achieve this, throughout the project I would be experimenting with the addition of flux, having forms that ooze and melt like dripping wax through and against the beautifully recognisable handles, lids and decorations. Capturing not the human narrative or landscapes traditional to Swansea porcelain ware, but of a material narrative. One of fluidity, transformation, and the unseen story within the kiln.

I began this project but first locating the technology that would allow me to capture the original ceramic objects within the archive, in which it was a great honour to handle. Thankfully, I was able to get my hands on a portable 3D scanner that was hand-held and allow me to transport my digital practice and set up a makeshift site within the ceramic archive. This 3D scanning technology isn’t the most reliable and doesn’t give the best quality scans in relation to other methods, but this was something I wanted to exploit in this project. With the scanner struggling to determine white glazed surfaced and the difference between gold surface decoration and texture.
The outcomes had a new quality to themselves, one that was reflective of the original object but also of the process of which it was captured. Emerging with multiples of the same handle and fragmented surfaces that would be suspended in space.
The challenge then was for me to digitally model these fragmented pieces into something that could be obtained in the physical world, one solid surface that could be 3D printed. This meant using my digital knowledge and flipping between software. I was able to model from reference images new forms that would be stitched together with the scans, with some success but some failures.
Alongside my digital practice. Where I seem to be battling with achieving things in the material world, very much in a material sense, I was testing bone china with the addition of flux. As previously mentioned, I was aiming to achieve unstable aspects of my work that oozed and melted. Through the addition of flux, silica, clay bodies become more glass-like and melt at lower temperatures. In order to get the right finish and the desired movement, I did a series of incremental tests. Although this has to be done with care, as the ceramic body will now melt and can course considerable damage to the kiln, as well as adhering itself to anything it comes into contact with.
While the material tests were underway, the printing of the objects had begun and for the first time, I was able to see the objects in the flesh and handle them. This is always a really exciting part for me and its always really interesting to touch and engage with something you have only ever seen images off. Similar to anyone that has studied or read about a piece of artwork before they encounter it in a gallery; its familiar but new at the same time.
With these new and existing objects, I can now start to arrange them, visual them in space and begin the next process of my practice, mould making. In order to make a mould, you first have to section up an object into pieces, where there are no undercuts for the plaster to get trapped. Though the use of clay, I section of each part as well as fill any gaps that within that void, the liquid plaster is poured. Between each section, a number of natches are carved in, and the mould is then washed with a protective soup that acts as a barrier for the next pouring of plaster. When all the sections are set, the mould is then left to dry.
This process is painstakingly precise and time-consuming, part of which I like, maybe in a sadistic way. The more time you put into claying up and the more precise the mould can be made, the better the finish of the objects. To also help with the mould making as well as the finish of the objects, some of the outcomes within the collection had to be made in sections. This way not only made it easier when printing but also less complex when moulded separately and assembled once cast in clay.
Without demonstrating the casting technique, it’s difficult to discuss all the many material problems bone china posed. I am still learning myself, how this material can react so much to environmental conditions and being handled at each step of the making.
In contradiction to the industrial process used to produce the original work, I chose to bisque the pieces to around 1020 °C, enough to allow porosity but also glaze fit. The work was then fired with a clear glazed finish to 1220 °C, any higher and the clay body would begin to warp and change shape under its own weight. The final glazed work was then carefully cleaned and the application of lustre to the details, leading to the third firing of 750°C. Just enough to adhere the lustre and soften the glaze, but not enough to affect the overall shape.
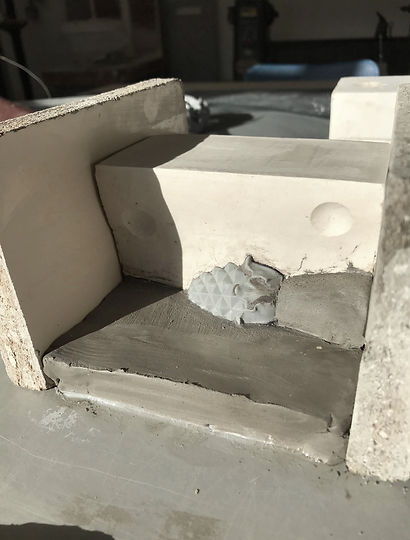
The Incubation project at Aberystwyth University has been a wonderful opportunity to be a part of; giving me the ability to connect with people that I may have otherwise never got the chance to collaborate with, as well as generating work alongside fellow friends and graduates of Cardiff School of Art and Design. I have been challenged within my ability to work with new material, bone china, as well as expanding my knowledge of glazes to generate texture and small decoration of lustre. I have also gained a better understanding of myself and processes that are integral to my practice; overcoming obstacles in a professional environment outside of an institution.
With regards to the work generated in response to the ceramic archive, I was able to exercise forgotten skills and processes previously learnt, combined in new and exciting ways, pushing my material knowledge further. One aspect I was looking to explore within this project was scale, working with larger pieces and prints than before. Through the combination of digital and traditional hand-skill processes from 3D printing, turning plaster on a lathe and hand building, I was able to generate multiple components that I hope to not only use to generate larger-scale objects but compose into one cohesive body of work. As this project is so short and fast-paced, the work has to be made with minimal testing and almost encouraged me to rely on my experience and gut instinct when making, which for me, added to the enjoyment.
This project will also require me to do a demonstration, which will explore the process of slip-cast, using the studio plaster moulds. I will explain different pouring techniques, timings for the clay and finishing techniques. This is a creative and fun workshop, focusing on experimentation. Experimenting with casting slip forms and how to join multiple clay objects, through the cutting and sticking, to give multiple possibilities and outcomes.
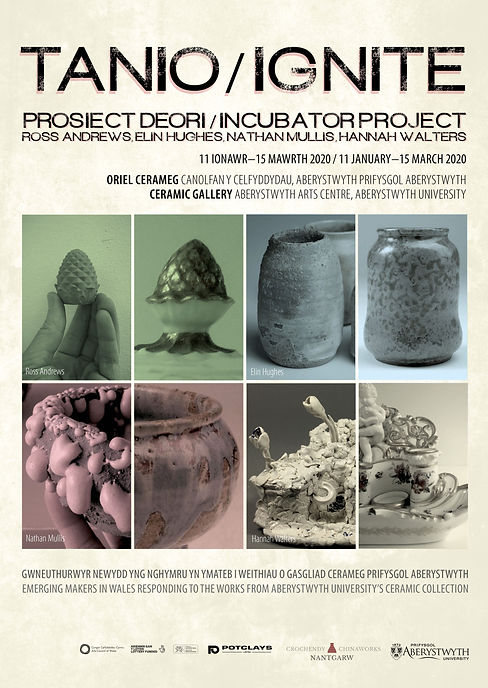
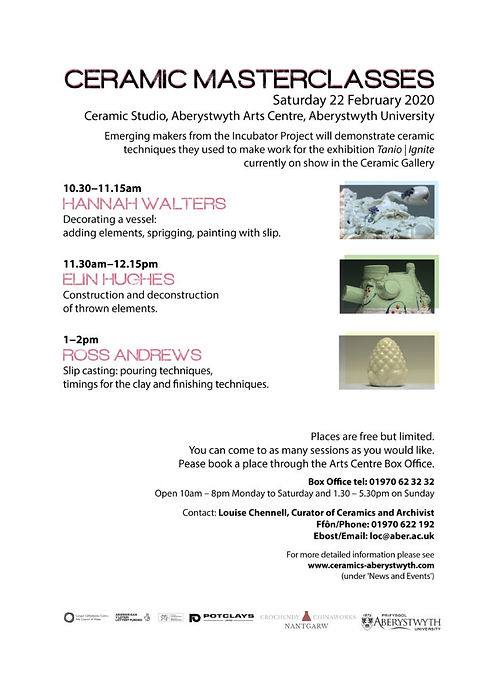
Like every project, I wouldn't say this project and outcomes are finished. I still want to push this project and concept more... so stay tuned and let's see where it goes next.